Lumen Calculation Guide: Optimize Your Facility Lighting
Proper illumination is crucial for the efficient and safe operation of any commercial or industrial facility. Whether it’s a manufacturing plant, warehouse, office building or other workspace, lighting plays a key role in productivity, compliance and well-being. However, determining the precise lighting needs can seem daunting without the right guidance. This article will list a step-by-step process for accurately calculating the total lumen output required for any commercial or industrial space.
Lighting in commercial and industrial spaces differs from residential settings in several important ways. Occupational Safety and Health Administration (OSHA) regulations establish minimum illumination levels for many workplace activities based on safety considerations. Adequate lighting is also vital to productivity as it affects visual tasks, worker morale and fatigue levels over long shifts. Furthermore, commercial lighting designs must account for fixtures suitable for high ceilings and potential obstructions from equipment or overhead structures.To learn more about how to effectively manage outdoor lighting and reduce energy costs, see " Lumen Secrets for Outdoor Spaces: Save Energy!" Guide
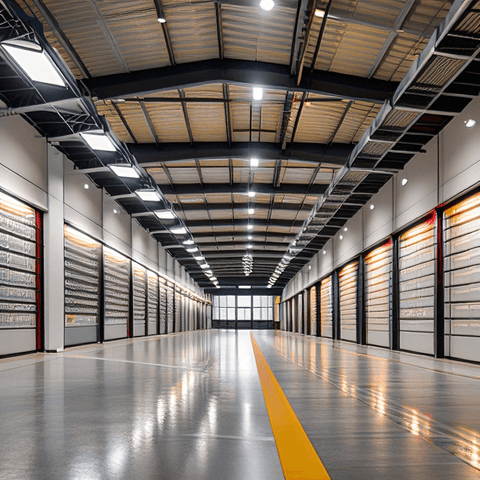
Given these operational differences, a one-size-fits-all approach will not suffice. Proper lumen calculations are needed to develop an optimized lighting layout for each unique workspace. Underspending on lighting can jeopardize safety and efficiency, while overinvestment is an unnecessary cost. The following guidelines provide a methodical process for accurately determining the total lumen output required by any commercial or industrial facility according to its specific needs.For those needing more depth into the specifics of lighting solutions, particularly LEDs, delve into the 'Mastering LED Lighting Standards In Industrial Spaces', which provides essential insights into maintaining compliance and efficiency with your LED selections.
1. Measure the Space
The first step is to precisely measure the dimensions of the area(s) that need to be lit. For large commercial or industrial facilities, the space may be segmented into defined work zones with different lighting needs. Use a laser distance measurer or tape measure to trace the perimeters and note any obstacles. Be sure to account for:
- Layout of workstations, equipment, and structures
- Ceiling height which affects fixture placement options
- Aisles and corridors for circulation
- Storage locations and racking systems
For multi-level facilities, measurements should be taken on each floor or mezzanine. Backrooms, offices and other supporting areas also require illumination and must be included in the calculations.
It’s also important to consider layout changes over time. Allow for future expansion possibilities by measuring larger buffer zones. Note any pending renovations that could impact lighting needs down the road.
Clearly document the measurements and develop a scaled floor plan denoting each segmented work zone. Note the length, width and height of each area. For irregularly shaped spaces, calculate the floor area using standard geometric formulas. Accurate space measurement forms the foundation for determining the specific lighting requirements.
With the areas precisely quantified, you can now select the appropriate recommended light levels based on the intended tasks and activities in each zone.
2.Determine Lighting Task Levels
Once spaces are measured, assign the appropriate recommended lighting task level to each segmented work zone. Proper illumination is essential to visual tasks and safety regulations dictate minimums.
There are three primary task levels applicable to commercial and industrial settings:
Low Activity Areas (50 lux/5 foot-candles)
- Office and administrative spaces
- Storage and warehouse aisles
- Janitorial and utility rooms
Medium Activity Areas (100 lux/10 foot-candles)
- Assembly and manufacturing zones
- Laboratory and inspection stations
- Loading docks and receiving areas
High Activity Areas (200 lux/20 foot-candles or more)
- Demanding visual tasks like inspections
- Heavy manufacturing with machinery
- Precise assembly and quality control
Refer to applicable codes like OSHA or IES standards to determine the recommended minimum lighting levels for each type of task in your facility. Consider both baseline and more demanding visual requirements over time.
Higher or supplemental task lighting may be needed for non-routine visual tasks. Emerging technologies are also allowing flexible, dynamically adjustable lighting to account for various on-demand visual needs.
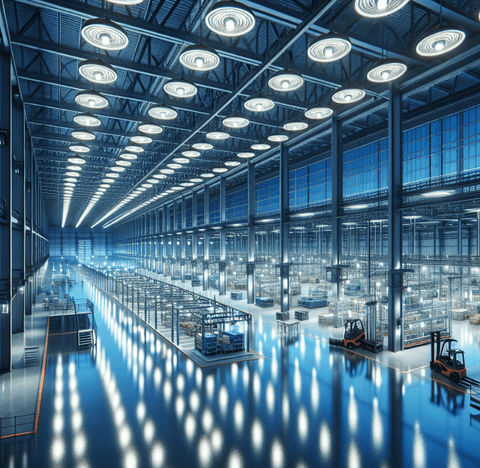
Document the assigned task level for each work zone on the floor plan. In the next step, these levels will form the basis for calculating the total lumen output requirement. Properly assessing lighting needs up front ensures compliance and optimizes workspace illumination.
3.Calculating Total Lumens
Now that spaces are measured and task levels assigned, the total lumen output can be calculated for each work zone.
For each area:
- Look up the lux/foot-candle recommendation based on the assigned task level
- Convert the measurement to lumens per square foot using standard conversion factors
- Multiply the square footage of the zone by the lumens per square foot requirement
For example:
- A loading bay measured at 20ft x 30ft = 600 sqft
- Loading docks are considered a Medium task area requiring 100 lux
- 100 lux converts to about 30 lumens/sqft
- So the loading bay would need 600 sqft x 30 lumens/sqft = 18,000 total lumens
Don’t forget to calculate lumens separately for each work zone and keep a running total. Consider adding 10-20% extra lumens if the space has:
- Dark wall/floor surfaces that absorb light
- Significant natural light that varies
- Potential future changes or expansions
Also account for any emergency lighting requirements from codes. Some facilities need dedicated nighttime illumination or backup lighting circuits.
Once complete calculations are done for every zone, add up the totals to determine the overall lumen output required for the entire facility. Proper lumen calculations up front help ensure the actual installed lighting solution meets operational needs. In the next section, this grand total can be used to select appropriate fixtures and bulbs. However, not all LEDs are created equal; the quality of your bulbs will greatly affect the longevity and performance of your lighting. How To Spot The Best Ones guide.
Conclusion
Proper lighting is essential for the safe, efficient operations of any industrial or commercial facility. By carefully measuring spaces, assessing task levels, and calculating total lumen requirements, facility managers can right-size their lighting design to optimally meet operational needs both now and in the future. Following the guidelines provided in this article ensures lighting specifications are properly engineered from the start.To explore a range of high-performance LED lighting products that cater to these precise specifications, consider the offerings from Halcon Lighting, which includes troffers, high bays, strips, panels, pendants, and more.